Effective controls in the construction industries are important to avoid workplace health hazards, injuries and illnesses, and accidents. It also enables employers to help workers in hazard identification and to be in compliance with OSHA health standards. According to the U.S. Bureau of Labor Statistics, 2.8 million nonfatal workplace illnesses and injuries were reported by private industry employers in 2022, an increase of 7.5 percent from 2021. The growth in diseases, up 26.1 percent to 460,700 cases, and injuries, up 4.5 percent to 2.3 million instances, is what is responsible for this surge.
The respiratory sickness cases, which increased by 35.4% to 365,000 cases in 2022, are the main cause of the increase in illnesses. This follows a decline in respiratory infections from 2020 to 2021. These nonfatal injuries can be avoided by the guidance provided on health hazards in construction OSHA.
OSHA construction also provides various courses to workplace exposure limits like OSHA 10 hour training and OSHA 30 Construction courses. If you are an employer in a construction company, then you must opt for training courses. They will allow you to do better health risk assessments and will also enable you to train your workers efficiently.
OSHA Health Hazards
In this guide, we will provide you with workplace safety tips and identification of the health hazards levels and how you can reduce the chances of risks by opting for the OSHA 30 construction and OSHA 10 training courses.
Work Safety Hazards
The most frequent dangers in a workplace or construction environment are those related to job safety. They could also be unique to a certain function. A construction employee, for instance, could use specialized equipment, raising particular safety issues for that occupation.
They are of the following types.
Spills: Any workplace may experience spills; therefore, coming up with a strategy to stop falls following a spill is crucial. You can place a caution sign outside to warn people to stay away from the area in order to lessen the chance of a spill danger.
Obstacles: There is a risk of tripping when there are obstructions in your way. These consist of obstructed aisles, cables lying on the ground, or misplaced equipment. Your business can design floor plans and procedures to arrange items in the least obstructive locations to reduce the chance of a spill. One way to lessen the chance of tripping is to relocate or conceal cords.
Electricity: it is also one of the health hazards in construction OSHA 30. This OSHA standard addresses safety measures to protect employees from the risk of electric shock. This includes teaching employees how to handle extension cables properly, using ground-fault circuit interrupters, and what to do if they come into contact with live electrical components. Electrical hazards pose a severe risk to construction workers.
Chemical Hazards
When an employee or worker comes into contact with chemicals in any form—solid, liquid, or gas—chemical dangers arise. Those who handle, produce, package, ship, or prepare chemical items fall under this category. Facilities are required by OSHA’s Hazard Communication Standard to maintain an inventory of every product.
These chemicals may include liquids like paints, acids, and other solvents, and gases including acetylene, propane, carbon monoxide, etc.
Physical Hazards
Environmental or physical hazards are dangers that can affect your body without necessarily coming into contact with it. Certain industries are more likely to experience these risks.
Professionals who work outside, for instance, could be more exposed to weather-related issues. OSHA health Vs physical hazards is important to identify the hazards in a workplace. There are different types of physical hazards like:
Noise: When workers in manufacturing or construction use noisy machinery, they run the danger of being exposed to loud noises. It is possible to mitigate the danger of spills by offering protective equipment like headphones and earplugs.
Temperature: Certain individuals, such as landscapers, roofers, and delivery drivers, may be required to operate in extreme cold or heat. You may design training programs like OSHA 10 and OSHA 30 training and control measures to assist personnel in identifying the symptoms of exposure, dehydration, and heatstroke in order to reduce the probability of a spill hazard.
Ergonomic Hazards
Workers who often lift, crouch, kneel, twist, grip, stretch, reach overhead, or engage in other unpleasant positions as part of their job activities may develop work-related musculoskeletal diseases (WMSDs).
OSHA’s 30-hour program includes preventative measures for musculoskeletal disorders in addition to covering ergonomic risks such as material handling and accidents involving repetitive motion.
Excavation and Trenching
Working in an uncovered trench is dangerous. The walls might collapse without warning. Employees are unable to move or make room for themselves when this happens.
The seminar examines the dangers associated with excavation and trenching, such as cave-ins and engulfment. It discusses the safety measures and safeguards that should be put in place to reduce these risks.
Tips for Mitigating the Health Hazards at a Workplace
Taking care of risks at work might be difficult. Nonetheless, a few broad rules or regulations can aid in preventing workplace hazards. Regarding the workplace risk rules of your firm, you might take the following actions:
Updating the Employees:
It’s critical to make sure your job instructions, safety protocols, and work regulations are current and contain all pertinent information. Encourage your workers to go for the OSHA training courses for a better understanding of the OSHA rules.
Availability:
All employees benefit most from having access to safety rules and procedures. Keeping both digital and hard documents at your office might help avert problems at work.
Enforcement and Awareness
It is advisable to periodically evaluate policies and the individuals enforcing them in order to confirm their efficacy. Mandatory training on a regular basis can aid in reminding staff members of crucial regulations that support their safety. Offering incentives to staff members for their involvement may help improve morale.
Conclusion
Every hazard has the capacity to affect the bodily and emotional well-being of others. You may take control measures like awareness campaigns, training, honest dialogue, and feedback to assist in lowering these risks. Discipline actions could be essential, if necessary, to keep people safe at work.
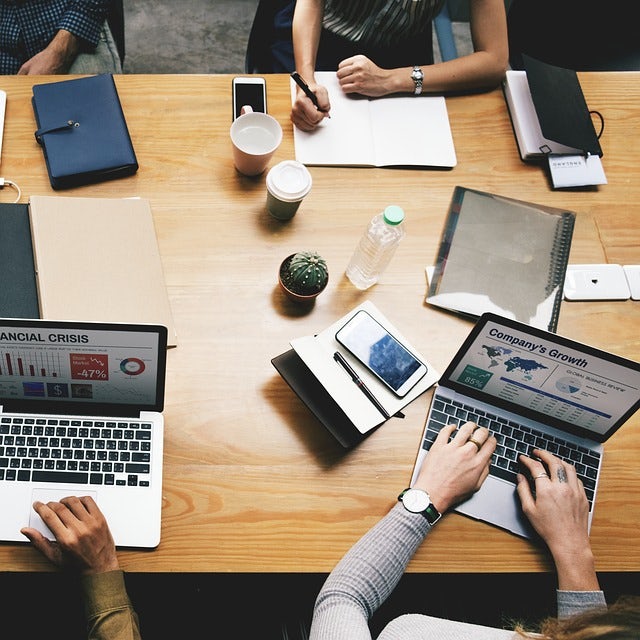
We’re a Digital Team from EngineTemplate with 5 content experts. Our team has 5 years exp in open source Joomla and WordPress, we make daily blogs and build useful resources for everyone who is having issues with open source while using it.